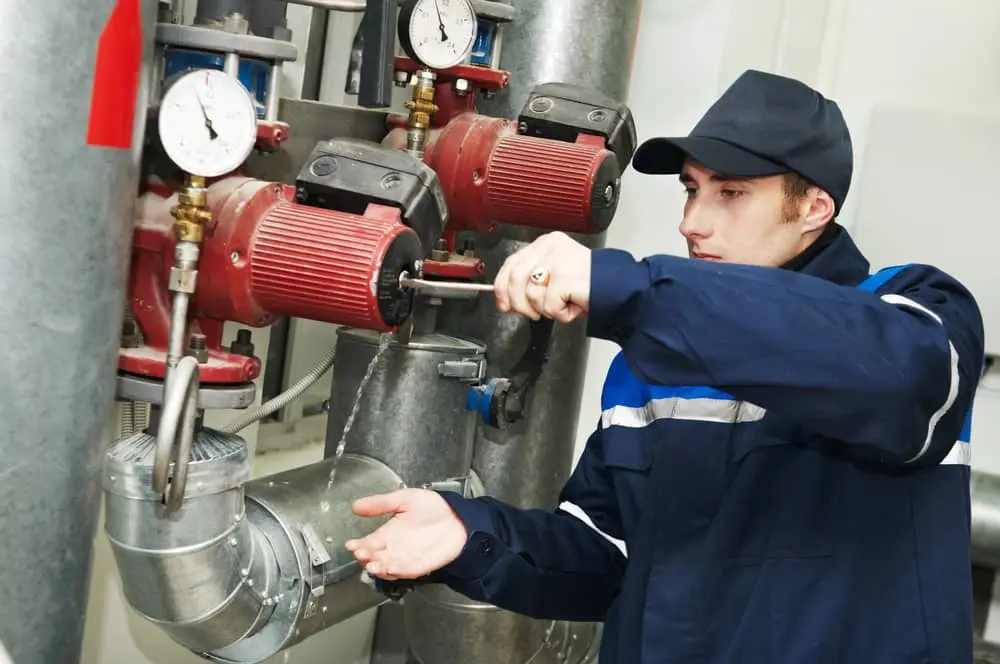
Taking Care of Your Water Pump: What Wears Out a Water Pump?
When you work in an industrial facility, one crucial piece of equipment that may need to be installed on your property is a water pump. These pumps are made to work harder than standard water pumps, making them perfect for industrial settings, so many clients ask us, โWhat wears out a water pump?โ.
These pumps are also designed to handle water and various additional liquids. There are numerous reasons why an industrial setting could use a water pump. For instance, these pumps are regularly used to take excess water from construction sites. They’re also useful in areas where flooding is common and stagnant water can cause issues with workflow.
Functions of Industrial Water Pumps
Industrial water pumps have many different functions, which allows them to be highly versatile in industrial settings. These pumps can:
- Remove excess water from construction sites
- Pump water away in areas that are usually flooded by heavy rains
- Get rid of water in areas where stagnant water causes costly disruptions of work
- Pump water to many different manufacturing processes, which extend from cooling and thermal processes to mining and power processes
The actual functions of your industrial water pump depend on the type you choose. If you want to send water to various manufacturing processes throughout the facility, you’ll likely need to obtain a large pump with enough space. However, they are not indestructible
Things To Check When Your Pump Doesn’t Work
Let’s take a look at five things you should check when your pump isn’t working correctly:
Power Source
If your pump has stopped working or is not operating to the levels you expect, it could be a power issue. Look at the factory specifications for your pump and ensure that it receives the correct electrical power supply to work properly. Ensure that all electrical wiring is in good condition, that there are no loose connections, and that the electrical current is reaching your pump in the first place. If you have an air-operated pump, ensure the compressor is in good working order.
Lastly, if you are using a mains supply, call in a professional to assess whether your mains electricity is stable or not. Surges and dips in supply can seriously affect pump performance; this is often a problem with dosing pumps. A surge protector can help.
Sound
One of the first tell-tale signs of an underperforming pump is its sound. A change in sound can alert you to an issue with your pump or system. If you hear popping sounds, especially near the impeller, you could be experiencing cavitation. This occurs when pressure changes within a liquid, causing tiny air pockets to form and then implode. This can seriously damage your pump, especially the impeller, so check to see if there have been any signs of cavitation, such as eroded material. While your pump will produce a natural hum, it should not make any strange noises; if it does, this indicates something is wrong.
Alignment & Leakage
Is your impeller aligned correctly? Is your piping correctly installed? A properly installed pump system does not overly vibrate. It does not generate excessive heat. If anything is leaking from your pump or fittings, this also indicates an issue. Depending on the media you are pumping, it could be a serious health and safety problem that must be rectified immediately.
Wear & Tear
No matter how rugged your pump system is, it will experience wear and tear in the future. How old are your components? How old is your pump? It might need replacing if you’ve had your pump for many years. Look for noticeable indications of wear and tear, such as residue or deposits within your system that have broken off your pump, pipe, valve, or fitting interiors. You only need to replace one component rather than the entire pump or piping system.
What Wears Out a Water Pump
-
Oversized Pump
It is essential to select the right-sized pump for the application โ yet many engineers select pumps that generate more head and flow than the application needs. Over time, the pumped fluid will deteriorate the casing and impeller, and the worn pump will eventually function within an acceptable performance range. However, the pump discharge should be throttled until the wear occurs, which wastes energy. If engineers were to choose a smaller pump with a protective coating to minimize the effects of corrosion and erosion, they could save on this energy loss.
If the pump remains the same, many issues can occur, but the design point changes, such as increased energy costs and cavitation.
-
The Motor was Wired Incorrectly
If the motor is wired incorrectly, the pump shaft can rotate counter to its needed directionโindicated on the pump’s bearing frame. While the pump will still operate, it will operate at a fraction of the flow and head indicated by the performance curve. If your pump is not generating the expected flow rate, check that the shaft is rotating in the right direction.
-
Degraded Bearings or Contaminated Lubricant
If a bearing fails, it leads to a drag on the motor, which needs more current to rotate at the designated speed and more energy to acquire the correct flow. So, although your pump might generate the specified flow and pressure, more energy is needed to rotate the shaft.
Cleaning industrial pumps can also contaminate bearing lubricant, eventually damaging the bearing. Protecting bearings from damage and lubricants from moisture is crucial to guarantee the efficiency and reliability of your pump.
-
Corroded or Eroded Impeller and Casing
The shape and casing of the impeller are vital for the pump’s proper functioning, influencing its ability to impart energy to the fluid. Corrosion, erosion, and instances where solids in the fluid flow at high speed can alter the shape of the impeller and its casing, affecting the pump’s efficiency over time. Although pumps are made with an allowance for corrosion, anything beyond these limits can influence the efficiency of the equipment.
Choose pumps made of corrosion and erosion-resistant materials containing enclosed impellers and wear rings, or provide hard casings, protective materials for impellers or rubber linings to avoid erosion.
-
Cavitation
Clogged strainers or filters, blockages in the pipe, or poor piping design can result in cavitation, usually indicated by a popping sound. Pump cavitation can result in excess energy use and severe problems for your pump system, such as damage to the impeller and the pump housing and decreased flow and pressure. Excessive vibration can also result in early seal and bearing failure if left untreated.
Water Pump Maintenance
The amount of pump maintenance you will be required to perform depends on the type of industrial water pump you choose. Since centrifugal pumps have only a few moving parts, they require little maintenance. On the other hand, the maintenance requirements for industrial water pumps are considerably more stringent. While industrial water pumps can last for a lengthy period, obtaining regular maintenance on the system should help prolong the unit’s life.
While the maintenance requirements for centrifugal systems are light, they should still be maintained regularly. These systems should receive their first oil change after 200 hours of operation. Any additional oil changes can occur after 2,000 hours of operation. The same is true of all other maintenance on the water pump. When considering a positive displacement pump, schedule maintenance every three months or 2,000 hours of operation. However, more consistent maintenance may be necessary to ensure the system remains efficient.
Maintaining industrial water pumps ensures they stay in peak condition and run consistently. It’s also important to understand that not performing maintenance could cause an issue to go unchecked, which may lead to significant damage to the system itself. When this damage occurs, the repair costs are much higher than the maintenance costs.
Knowing the Facts About Water Pumps
Understanding the causes behind water pump wear-out empowers equipment operators to extend the pump’s lifespan proactively. Regular maintenance, proper filtration systems, careful operation within recommended parameters, and monitoring of abrasive and sediment materials are essential to mitigate wear-out. By addressing these factors, you can prolong the longevity of the water pump, optimize its performance, and ensure the efficiency of your operations for years to come.