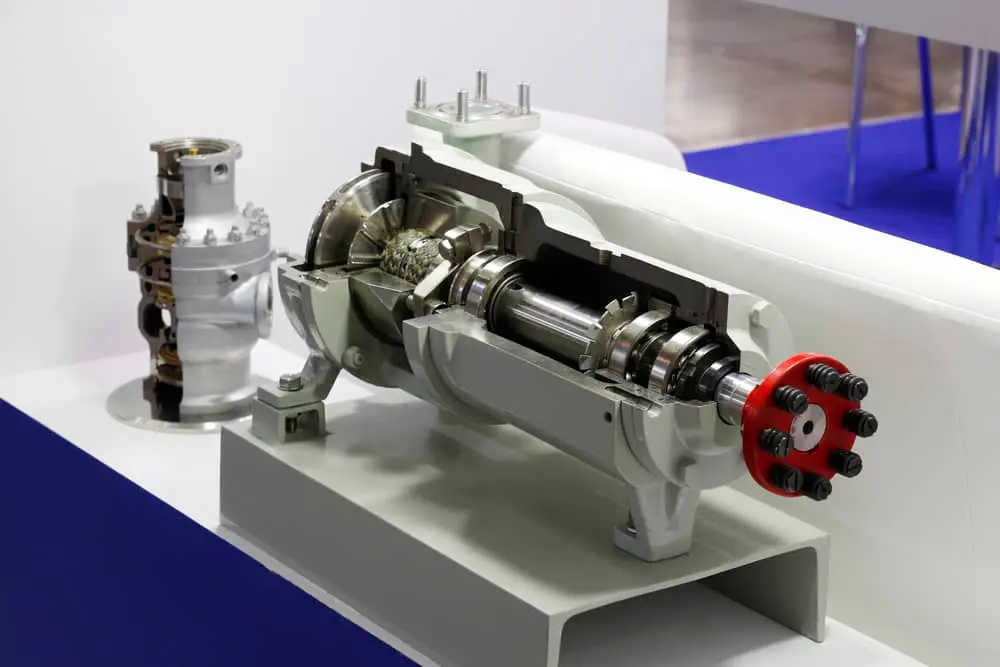
Preventing Devastating Downtime and System Failure: What Happens When a Mechanical Seal Fails?
Years ago, most pump shafts were sealed with rings of soft packing, compressed using a packing gland, yet this type of shaft seal needed a fair volume of leakage to lubricate the packing and keep it cool.
Then, with the development of the mechanical seal, which accomplishes restraining product leakage around the pump shaft with two flat surfaces (one stationary and one rotating). Although these mechanical seal faces require some leakage across their faces, they usually evaporate and are not noticeable.
However, due to the delicate components utilized for this new sealing process, mechanical seal failures are the main cause of pump downtime. To avoid this, it is essential to apply the right seal for the appropriate and desired function. But have you ever wondered what happens when a mechanical seal fails?
A mechanical seal can be exposed to a vast range of operating conditionsโsometimes very different from the conditions it was intended forโwhich can cause issues down the line. However, even if your seal is the appropriate one for the job, there can be times when it fails quicker than anticipated.
When this happens, you must act quickly to identify the cause of leakageโevery minute of downtime results in lost production and maintenance fees.
Understanding the Roots: What is the Main Cause of Mechanical Seal Failure
Mechanical seal failure often occurs, but why? Here are the main reasons for a mechanical seal failing within a process:
Dry Running
Dry running is when a pump is operated without fluid. This means internal parts that often rely on the pumped liquid for lubrication and cooling are subject to high friction and heat, leading to prompt failure. Failure can happen in seconds, so ensuring the pump is filled with fluid before operation is always important.
Tip: If a seal has been dry run, its face will be white, and to prevent dry running, an AMP sensor can detect when high amounts of AMPs are being drawn and stop pump operation before too much damage happens.
Chemical Attack
Every material has its formidable foe. A liquid incompatible with a fluid can cause internal parts like rubber seals, gaskets, pump casings, impellers, and diffusers to crack, contract, swell, or deteriorate.
Chemical compatibility tables show which materials work well with different fluids, rating them Good to Poor. This is one of the first items to be checked whenever frequent pump wear occurs or should pump failure occur after a short time.
Cavitation
Centrifugal pumps are controlled by the system they work in. If not restrained, they can perform actions that damage internal parts โ like driving a car downhill in first gear at speeds, with the rev counter in the red.
Operating a pump at the wrong components of a performance curve can accelerate part wear, wherein one can be the seal.
Excess Heat
Excessive heat due to very high fluid temperatures can cause elastomers to swell or melt, limiting their effectiveness and resulting in leaks.
High fluid temperatures not only originate from the process but if fluid recirculation happens for extended periods either because of operation against a closed valve or if fluid continues to recirculate via a relief valve, energy is transmitted to the fluid, causing fluid heating.
Incorrect Fitting
When installed, a seal is designed to move with the shaft. Lateral and vertical movement is normal. If installed incorrectly, excess play can lead to damaging forces to the seal. Once too restricted, the seal springs can snap, or faces can wear.
Shaft Movement Because of Bearing Wear
If a shaft has excessive play, its lateral movements will make the seal absorb such forces instead of the bearings – something it’s not designed to do. High torsional forces can tear the seal.
Worn Shaft or Wear
Certain elastomers can increase shaft wear, indicating when a seal is replaced, if the shaft has a smaller OD reduced by friction over the years, the seal will not fit tightly, enabling fluid to leak.
Solid Ingress
Seals are specifically made for a pumping process. Should a seal encounter solid particles like sand or silt that it is not designed to handle, grooves can form in soft seal faces, resulting in the seal leaking and dripping the process medium.
Installing a hard-faced mechanical seal can limit and prevent this problem from reoccurring, provided concentrations of solids are not above those specified at the inquiry stage.
Operator Error
Skipping initial start-up procedures and installation mistakes are big factors in mechanical seal failure. Improperly starting the pump can lead to the shaft twisting and the motor tripping, causing orbital movement, leading to internal parts contact, seal failure, and shortened bearing life.
Improper installation of the mechanical seal will cause damage to elastomers (o-rings or boots), together with a wide variety of other issues, as seen to the right. Mechanical seals can be relatively sensitive because the faces are very flat. Even a small amount of oil, dirt, and fingerprints can cause the faces not to align.
Completely Omitting Or Improper Use Mechanical Seal Flush Plans
A mechanical seal flush plan should be properly in place. The mechanical seal recommendation is complete with a coordinating flush plan.
Be aware: If there is no flush plan, dewatered product, and contaminants can accumulate, causing excessive heat or erosion on the seal and resulting in shortened seal life.
Selecting The Wrong Mechanical Seal Or Materials
Lack of knowledge and information accounts for most mechaniยญcal seal installation errors. Consider normal operating conditions, the potential for off-design and non-process activities, such as cleaning, steaming, acid, and caustic flushes. The picture to the right exemplifies poor material choice for an abrasive liquid.
What Happens When a Mechanical Seal Fails?
Mechanical seal failure affects many pump parts, including the pump shaft. Here’s what happens when a mechanical seal fails:
Sleeve / Shaft Wear
When mechanical seals fail, they spin on the shaft or shaft sleeve. Grooves wear into the metal and require replacement. Once they’re worn, they should not be re-used.
Gouging, Denting, Scratching Of Shaft
If there’s a catastrophic failure and shattered seal faces, silica carbide or tungsten bits can gouge, dent, or scratch the sleeve or shaft. Sliding a new seal above the damaged shaft surface will destroy the new o-ring on the seal, setting the seal up to fail from the start.
Corrosion Of Seal Shaft
During a long-term seal failure, where the seal leaks or drips small amounts of fluid, the shaft can become corroded and weaken.
Flashing Or Etching
Flashing or etching occurs most often when the fluid is hot or in a boiler feed application.
Fretting
Fretting is wear caused by the movement of the mechanical seal. If the seal is improperly installed or the seal faces are damaged, a great deal of movement will happen, causing fretting on the shaft.
If a mechanical seal has failed and damaged the pump shaft, it’s best to replace it. Using a damaged shaft or sleeve will cause more issues and will most certainly become a more costly repair.
In conclusion, mechanical seal failure is usually a combination of various factors: lack of lubrication at seal faces, improper selection, operator error, etc. By taking proper measures, such failures could be avoided, leading to more uptime and more production.
If you frequently experience mechanical seal failure and want to eliminate it from your process, speak to us to see how we can help.