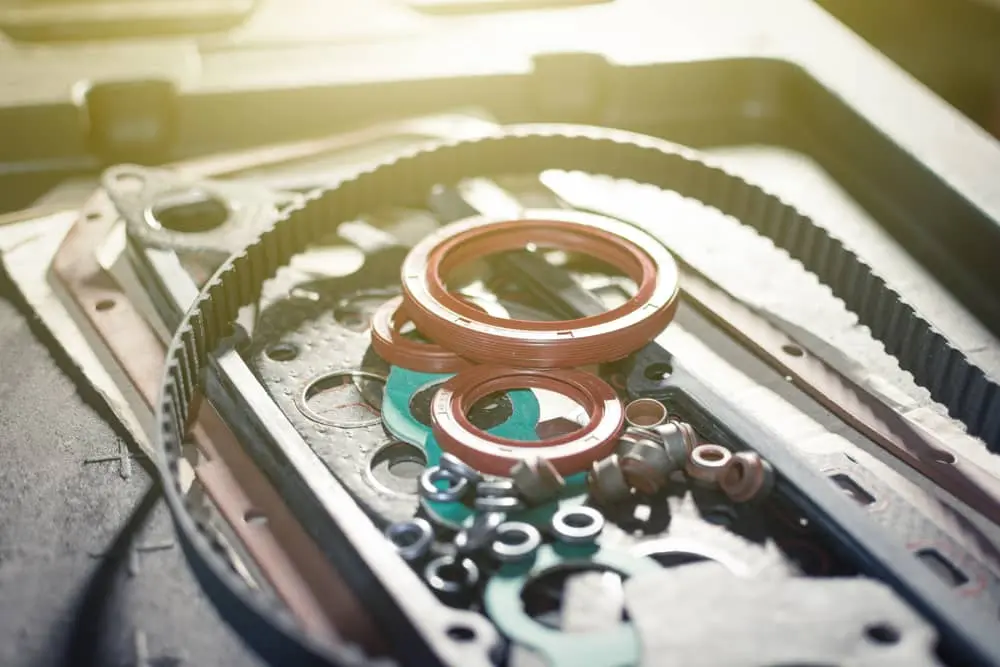
Tips from the Experts: How Do I Choose a Mechanical Seal for My Pump?
Mechanical seals can work for many years without issue if properly selected for their application. One must determine the application data (or operating conditions) to properly choose the type of seal and construction materials to ensure the seal’s maximum performance over its lifetime. โHow do I choose a mechanical seal for my pump?โ you ask? Here, we outline the operating conditions and discuss which material properties to consider to avoid choosing the wrong one.
Types of Seals Mechanical Seals Available
We will begin with the type of seal you should be using. Seals fall into many categories:
Hydraulically Balanced Seals
Hydraulically balanced seals are the primary type to use because they generate less heat and can handle a wide range of pressure and a reasonable vacuum.
If the pump suction pressure (not discharge) exceeds 400psi (28 bar), you might need a special version of a balanced seal.
Likewise, if a vacuum on the suction side of the pump measures less than one “torr,” you must go to a seal with no elastomers because elastomers “outgas” and shrink as the air is pulled out of the compound. This shrinking will cause the elastomers to leak, and the vacuum can be destroyed.
Stationary Seal
The stationary version of the seal is the best design because it will compensate for misalignment between the pump and its driver and the stuffing box’s not being square or perpendicular to the rotating shaft.
This type of seal also has some real advantages if you convert a packed pump to a mechanical seal or run at greater than electric motor speeds.
Metal Bellows Seals
Metal bellows seals should be selected if the product temperature is more than 400ยฐF (200ยฐC) and the stuffing box cannot be cooled. They are also a good choice for cryogenic (cold) service.
Remember that petroleum products must be cooled because they will “coke or carbonize,” open the seal faces, and clog up seal components. Metal bellows seals are also a logical choice if no elastomers are allowed in the system.
Dual Seals
Dual seals are becoming very important because of fugitive emissions laws. They can also be a spare seal if you cannot afford an unexpected shutdown. Dual seals should always be designed with a “two-way” hydraulic balance.
Non-Metallic Seals
Non-metallic seals should be selected if the pump wetted parts are manufactured from non-metallic material such as carbon, Teflon, plastic, etc. These seals are normally mounted as outside seals and have no metal parts exposed to the fluid you are sealing.
Do not depend upon a flush into the stuffing box to protect the seal materials against corrosion, and do not try to second-guess the application engineer who selected a non-metallic pump for this application. Stick with a non-metallic seal design in all non-metallic pumps unless you are a corrosion expert willing to select the correct metal for the application.
Cartridge Seals
Cartridge seals are necessary for ease of installation and for making pump impeller adjustments without changing the seal face loading, but some have problems. Cartridge seals also allow you to compensate for the shaft’s thermal growth.
Be aware that there are special precautions if you use cartridge-mounted stationary seals.
Split Seals
Split seals can be used in most applications today, especially the larger shaft sizes. In most cases, you can solve the packing conversion or seal leakage problem without taking the pump apart and causing a lot of downtime.
Split seals are the only real alternative to cartridge seal designs. Today, they are available in both rotating and stationary versions.
Most products contain solids, so the seal should have built-in slurry features. Except for most finished products, accept that you are pumping a slurry.
Be sure that the brand of seal you select will not damage the pump shaft. This will allow you to use solid shafts instead of the inferior-sleeved version with high L3/D4.
How Do I Choose a Mechanical Seal for My Pump: Factors to Consider
Liquid Handled
The first step in the seal selection process is identifying the exact liquid being handled. The seal material must withstand the fluid it processes. Every seal material needs to be chemically compatible with the fluid, otherwise, there is a higher chance of seal failure occurring.
Pressure Inside the Seal Chamber
The pressure inside the seal chamber and the size of the seal decide whether a balanced or unbalanced seal is needed.
Temperature
Seal materials must be selected to handle the liquid’s temperature appropriately. Temperature is important since different seal materials are rated for certain temperatures, and you should stay within these materials’ temperature limits.
Viscosity of the Liquid
Knowing the liquid’s viscosity is important to ensure appropriate seal life. Abrasive liquids can create excessive wear and ultimately shorten the seal’s life. Double seals or the use of an external flush plan give operators the option to use mechanical seals on these difficult fluids.
Reliability & Emission Concerns
Every company has its own standards and operating procedures regarding an application’s reliability and emission concerns. The seal type and arrangement must meet the pump application’s desired reliability and emission standards. Because environmental safety is now a major concern for manufacturing companies, double seals are emerging as the preferred solution.
Design Choices for Mechanical Seals
Seal design choices include pusher, metal bellows, and elastomeric bellows.
A pusher mechanical seal utilizes a dynamic secondary seal or o-ring to seal the fluid path between the pump shaft and the inner diameter of the spinning seal face. The secondary seals move axially along a sleeve or shaft to maintain contact at the seal faces, compensating for seal face wear and any seal wobbles due to misalignment.
The metal bellows design is a non-pusher seal design. The secondary seal in a non-pusher design does not have to move along the shaft or sleeve to maintain seal-face contact. The bellows itself provides the necessary spring loading for seal face contact. Metal bellows provide effective sealing in various temperatures and use no elastomers. Mechanical seals image
An elastomer bellows seal is a non-pusher seal design in which a single spring coil fits over the shaft and bellows.
Specifications for Mechanical Seals
Other important design parameters for mechanical seals include spring, shaft mounting, and seal configuration.
Spring configuration can be single or multi. Single springs are sometimes called “monoclonal” or “single-coil” designs. This type of seal uses a large spring cross-section that resists corrosion. Its chief limitations are its tendency to distort at high surface speeds, the large axial and radial space required, and the need to stock a different spring size for each seal. Multiple small springs are not as susceptible to distortion at high speeds as single coil springs and consequently exert an even closing pressure on the seal ring at all times.
Shaft mounting choices include cartridge unit, noncartridge, split seal (fully split), and semi-split seal.
The seal can be tandem, face-to-face, back-to-back, or concentric.
Applications
Common applications for mechanical seals include pumps, agitators or mixers, marine stern tubes (propeller shafts), gas seals (spiral groove seals), and cryogenic seals.
The seal can be mounted internally or externally. Important shaft size and service limits to consider when searching for mechanical seals include nominal shaft diameter, shaft speed, alternate shaft or rubbing speed, operating pressure, and operating temperature.
Common features of mechanical seals include balanced or unbalanced construction, dependability on the direction of rotation or independence of direction of rotation, capability to handle slurries, and an encased spring element.
The direction of the shaft rotation is important to consider. This is the direction of a shaft’s rotation, as seen from the drive. Mechanical seals that are dependent on the direction of rotation are those that transmit torque using a conical spring or those that are equipped with a pumping screw. The direction can be clockwise or counter-clockwise.
Material Consideration
After choosing the seal type, we must select the seal materials. Usually, you will choose three different materials.
The Metal Components
You are concerned only about the parts that get wet in the fluid unless the pump is in a very corrosive atmosphere. Wetted parts include the pump volute, impeller, shaft or sleeve, mechanical seal, stuffing box, etc.
Carbon/graphite manufacturers supply a carbon/graphite chart that will give you the details of any particular grade they manufacture. With few exceptions, an unfilled carbon such as Pure grade 658 RC is always a safe choice if any grade of carbon is acceptable in your fluid.
The Hard Face
There are many to choose from, but self-sintered silicon carbide is your first choice. Reaction-bonded silicon carbide is also popular but can be attacked by many high-pH fluids. The common cleaner “caustic” is a fluid that will attack reaction bonded silicon carbide.
The rubber parts (elastomers) that are exposed to the fluid
The dynamic O-ring (the one that flexes and rolls) is the most critical.
Most chemicals and chemical combinations can be sealed with a good grade of Viton of ethylene propylene. Most solvents and a few other chemical combinations require something a little better. The super elastomers have just about replaced Teflonยฎ in those applications, but they cannot be used everywhere.
Remember also that all elastomers have an upper and lower temperature limit that must not be exceeded.
You must choose seal materials chemically compatible with all the fluids passing through the equipment, including any cleaners or solvents that might flush through the lines.
This is especially critical when choosing an elastomer (O-ring). The combination of metal parts and face is usually compatible with most cleaners and solvents.
Do you want to learn more about mechanical seals? Please reach out to us today!