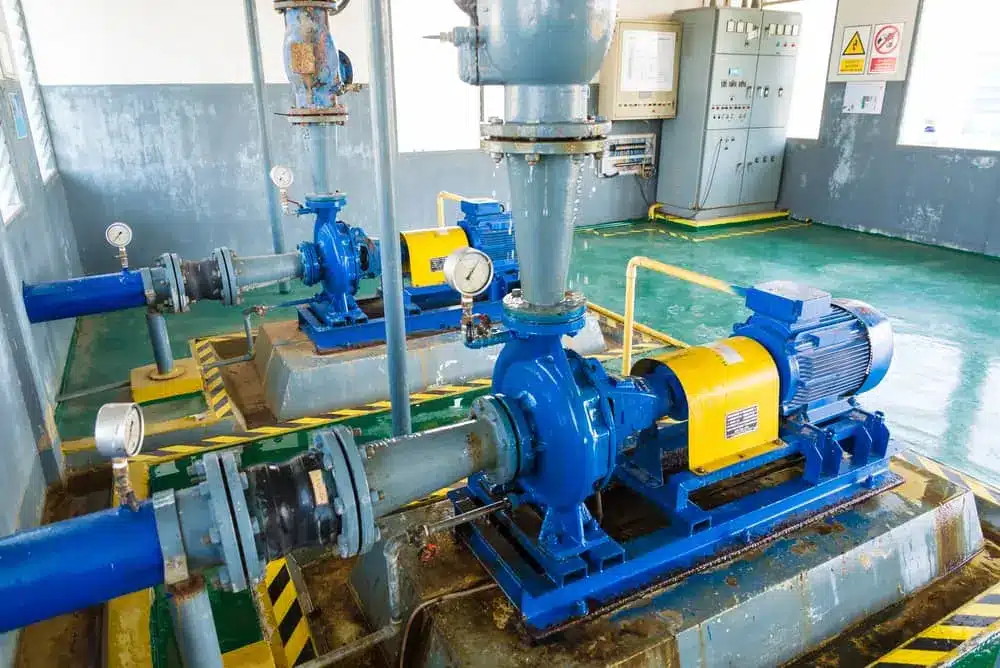
Understanding the Longevity of Mechanical Seals: How Long Do Pump Seals Last?
How long do pump seals last? Various factors determine seal life, many independent of the seal design. Installation issues, improper pump operation, and an inadequate seal support system are just a few.
A mechanical seal retains a liquid or gas inside a rotating piece of equipment. Mechanical seals can be designed to prevent the process from being contaminated by the environment or from leaking into it.
The essential components of a mechanical seal are a Rotating Part and a Stationary Part. The primary seal consists of a rotating face and a stationary face. A thin film of fluid keeps the faces lubricated.
A tiny gap between these two components creates a restrictive flow path.
Other components, namely o-rings or gaskets, are used as secondary seals, and hardware is used to support the seal faces and attach them to the rotating part (e.g., shaft) and stationary part (e.g., cover plate).
What are the types of Mechanical Seals?
Single Seal
It consists of one primary seal. There is always some leakage either into the atmosphere or the process, depending on the pressure.
Double Seal (Barrier)
It has two primary seals in various arrangements. A barrier fluid is between the two primary seals, which is at a higher pressure than the process. There is always some barrier fluid leakage in the process and out to the atmosphere.
As long as barrier pressure is maintained, there is no leakage of the process into the atmosphere or contamination of the process by the environment.
Double Seal (Barrier)โWet
It is a double seal where the barrier is a liquid. It is generally the most robust seal and has good pressure, speed, and temperature capabilities.
Double Seal (Barrier)โDry
It is a double seal in which the barrier fluid is a gas. There are two specific types: contacting and non-contacting.
Gas Contacting Seal
The seal faces are in contact, and the soft face wear acts as a lubricant: low pressure, speed, and temperature capabilities and possibilities of wear getting into the process.
Gas Non-Contacting Seal
The seal faces are NOT in contact. A gas flow between the faces keeps them apart: suitable temperature, speed, and pressure capabilities. If operated correctly, there is no wear, but care must be taken to minimize shaft runout.
Component Seal
It is where both the rotating & stationary hardware are connected separately to the pump/mixer.
Cartridge Seal
It is where the rotating and the stationary hardware are pre-assembled before mounting onto the pump/mixer. Cartridge seals are much easier to fit & maintain compared to the component seal.
What Causes a Mechanical Seal to Leak?
Mechanical pump seals leak once the faces are forced apart. If there’s evidence of product leaking from a mechanical seal, the faces have had cause to separate. The challenge to maintainers is to find the cause and rectify it.
Below are some of the common causes of face separation.
- Pressure hammer within the equipment caused by such occurrences as rapid closure of valves somewhere in the process.
- Solids/dirt pinned between the seal faces during assembly or a pressure surge.
- Crystal build-up on the seal faces as crystallizing products seep past the running faces.
- Seal faces run dry and build heat and crack due to nil or poor lubrication.
- Underloaded springs/bellows push on the rotary seal when the seal is set up on the shaft.6 Unequal spring force on the rotary seal due to damaged or jammed springs/bellows.
- Unequal spring force on the rotary seal due to damaged or jammed springs/bellows.
- Movement of the rotary seal housing along the shaft if the locking screw loosens.
- The seal was damaged during installation and needs to be corrected.
- The mechanical seal configuration can promote the loss of liquid from the mechanical seal.
How Long Do Pump Seals Last?
When deciding what kind of seal is best for a given application, choosing one that will last the longest is best. It’s impossible to tell precisely how long a seal will last, but knowing what forces wear down seals โ and the materials that best stand up to such forces โ will ensure that your seals have the most extended life possible.
Sometimes, it’s possible to create a general idea of how long a seal might last based on similar applications, although this is only an estimate. The only way to find out how long a particular seal will last is to put it into a specific application and measure how long it takes for the seals to fail, plus averaging it out over time.
The high end of this spectrum tends to be around three years, with some highly robust operations being much shorter. Allowing a seal to run until it fails can lead to catastrophic consequences, major failure, and product loss. It’s imperative to err on the side of caution when replacing seals.
Shelf life is another story. Most seals have an expected shelf life that can be much more accurate than application life duration estimates. Higher quality seals will degrade much slower over time than cheap knock-offs. Rubbers have a shelf life of around fifteen years. Fluorocarbons and silicone have much longer shelf lives, lessening much slower than any timeline relevant to business.
The most common reasons and forces that act upon seals leading to failure and shorter lifespans are much more readily available and preventable than guessing a given seal’s life span in a specific application.
Initial Failure
If a seal fails much quicker than expected, chances are the wrong seal was chosen. When selecting a seal, the correct material must be chosen. Many fluids seals must contain within their systems are corrosive or reactive to certain seal materials, causing them to weaken much faster. There are other reasons for a quick failure.
It also may need to be the correct application shape, size, or design. If a seal is designed for static applications and put into a dynamic operation, it will fail much faster than intended. This is why it is so important to have an expert on seals guide you through the selection process, as these failures can be extremely costly due to the loss of product, damaged machinery, and lost time.
Random Failure
A random failure typically occurs when the conditions surrounding a seal change. The most common cause is a mechanical or procedural failure that precipitates a large amount of strain on the seal. A rapid increase in pressure, temperature, or physical force on the seal could also be a cause. These issues are more mechanical than sealing problems; unless these changes are routine and expected, the seal must withstand both force ranges.
Environmental factors can also cause these types of failures. If the machine’s location is exposed to the elements, a change in seasons or weather can greatly impact a seal’s ability to withstand the forces acting upon it.
Wear Failure
The aim of all operations is a seal that predictably degrades over time. If a seal has a relatively predictable lifetime, it can be replaced to prevent failure, and there is no loss outside of the small amount of time it takes to change the seal.
Finding the Right Seal
All of this comes down to finding the best seal for your application. Heat, pressure, chemical composition, and other factors influence how long a seal might last, so it’s best to have an expert to compensate for the forces acting on it.
We at Platinum Performance Products are experts in the sealing industry and can point you to or design the seal with the best potential for a long lifespan in your application. Contact us today to find the proper seal for your operations.