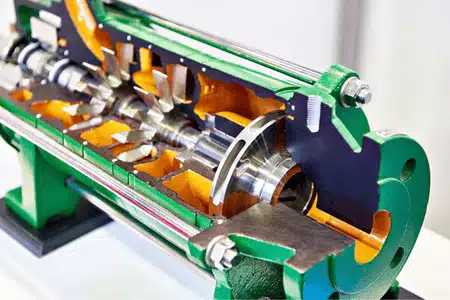
Pump Packing Replacement: Identifying the Perfect Time to Act
Pump packing serves as a critical seal in industrial pumps. These braided rope-like rings, often made with graphite, sit in the stuffing box around the shaft to prevent fluid leak and block gasses or chemicals from escaping. Proper pump packing ensures systems run with minimal loss and optimal safety.
When packing wears out, pumps lose efficiency and create safety hazards. Leaks can worsen if valve settings or screw tension is incorrect, or if teams don’t follow replacement instructions. Teams should also inspect packing rings to make sure they fit properly and don’t allow fluid bypass.
Knowing when to replace pump packing helps teams avoid costly downtime and equipment damage. If you notice a persistent leak or the need to frequently wrap more material, it may signal deterioration. Following the proper method to wrap new packing, using approved pump packing and maintaining the right packing rings, keeps the system sealed and efficient.
Why Timely Pump Packing Replacement Matters
Packing rings create a seal around the pump shaft to contain process fluids. As they wear, leakage increases and pump performance drops. Ignoring worn packing leads to wasted product, safety risks, and potential pump damage. Water running from a leaking pump can damage bearings or motors, causing secondary failures if valve seals are compromised or if pump packing installation is incorrect.
Modern upkeeping focuses on replacing parts before they fail completely. Compression packing, often made of graphite or PTFE, should be serviced before catastrophic failure occurs. Most packing lasts 6 to 12 months under normal conditions. Harsh environments with abrasive fluids or high speeds reduce this lifespan significantly and demand careful pump packing installation procedures. Following proper pump packing installation steps and choosing the right seal materials is vital.
Key Signs It’s Time to Replace Pump Packing
Packing typically fails gradually, not suddenly. That gives time to plan pump packing substitution during routine maintenance rather than face unplanned downtime.
Excessive Leakage
A slow leakage rate is normal to lubricate and cool the stuffing box. But when water running increases or sprays from the pump housing, it means the packing has been exhausted. If tweaking the gland nuts no longer control it, it’s time to replace.
Visible Wear or Damage
Old packing becomes brittle, glazed, or frayed. Cracked or hardened individual rings lose their ability to seal. If you spot uneven compression, graphite dust, or material that looks burned from high temperature, plan a replacement.
Difficulty Maintaining Adjustment
When you’re always reaching for a screwdriver to tighten the packing, and the gland is fully compressed, the rings can’t expand further. If you adjust but lose control quickly, you’re better off replacing than overtightening.
Overheating or Temperature Issues
The stuffing box should feel cold, not hot. If there’s steam, smoke, or visible air bubbling at the drain, either the packing is too tight, not lubricated, or simply worn out. Conversely, a box that’s too cold may mean the seal has failed.
Unusual Noises or Vibration
High-pitched squeals or chattering come from rope packing rubbing dry against the shaft. Vibrations and shifting pressure often accompany these sounds, indicating damage to materials and the need for substitution.
Loss of Lubrication
Packing material often includes ptfe, oil, or flexible graphite. Without a proper lubricant, pump operation creates heat. Lubrication failure leads to burning, squealing, and a short life.
Abrasive Media Effects
Solids in the fluid wear out packing rings quickly. Sand or crystals create grooves and embed in existing packing, signaling poor preservation or missing filtration.
Installation Problems
Improper installation, like failing to stagger joints or using the wrong materials, makes even the highest quality products fail. Follow instructions, use the best way to install, and make sure the packing is tightened correctly.
Pump Condition Issues
A misaligned shaft or failing valve damages equipment and packing alike. Always inspect before you rebuild to avoid premature failure.
Best Practices for Pump Packing Installation
Proper installation is crucial for achieving maximum packing life and reliable sealing.
Safety and Preparation
Schedule pump downtime and isolate the equipment completely. Lock out power and close inlet and outlet valves. Relieve system pressure and allow the pump to bring to safe temperatures. Wear appropriate protective gear, especially when handling hazardous fluids.
Remove Old Packing
Loosen gland nuts and slide the follower back. Use proper packing removal tools to extract every ring from the stuffing box. Avoid scratching the shaft or box bore during removal. Thoroughly clean the stuffing box, removing all residue and old lubricant. Complete removal and cleaning are essential for proper new packing performance.
Component Inspection
Examine the shaft or sleeve for grooves, scratches, or corrosion where packing contacts the surface. Replace or repair heavily scored sleeves before installing new packing. Check the stuffing box bore and ensure flush ports are clear. Fix any mechanical issues like misalignment before proceeding.
Material Selection and Cutting
Choose packing material that matches service requirements including fluid type, temperature, pressure, and shaft speed. Flexible graphite works well for high temperatures and steam. PTFE excels with corrosive chemicals. Cut individual rings to proper size using the shaft as a guide. Make clean 45-degree or straight cuts so ring ends meet without gaps or overlap.
Ring Installation
Apply light assembly lubricant if recommended by the manufacturer. Install rings one at a time, seating each fully before adding the next. Stagger the joints so cuts are offset around the shaft to prevent direct leakage paths. If using a lantern ring for flush water, position it correctly in the stack. Install all rings with proper spacing and alignment.
Initial Adjustment
Reinstall the gland follower and tighten nuts finger-tight to gently compress the packing stack. Add slight additional compression but avoid over-tightening initially. The packing needs break-in time to conform to the shaft.
Startup and Break-In
Start the pump and observe the stuffing box immediately. Expect some leakage for cooling and oiling. Gradually tighten the nuts to achieve steady dripping at about 40-60 drops per minute. Never tighten to zero leakage as this causes overheating. Monitor temperature to ensure the stuffing box feels warm but not excessively hot. Adjust evenly to maintain uniform pressure.
Follow-Up
Recheck packing after several hours of operation as it settles. Make minor adjustments to maintain proper leakage rate. Monitor for abnormal behavior like smoking or complete leakage stoppage. Well-installed packing should require only infrequent regulations during its service life.
Extending Packing Life
Maximize time between replacements through proper monitoring and upkeep practices. Train operators to inspect stuffing boxes during routine rounds. Look for changes in leakage patterns that indicate regulation needs. Use packing materials suited to specific service conditions rather than generic options.
Keep spare packing and proper tools readily available to minimize downtime. Consider system factors that affect packing life like pump alignment, vibration levels, and flush water systems. Maintain chilling and flush systems at proper pressure and flow rates.
Conclusion
Successful replacement of pump packing depends on recognizing warning signs and following proper installation procedures. Monitor for excessive leakage, visible wear, temperature problems, and unusual noises. When replacement is needed, use appropriate materials and install them correctly with proper break-in procedures. Remember that packed pumps should always leak slightly for lubrication and cooling. With careful attention to timing and technique, packing replacement becomes a routine maintenance task that keeps pumps running safely and efficiently.