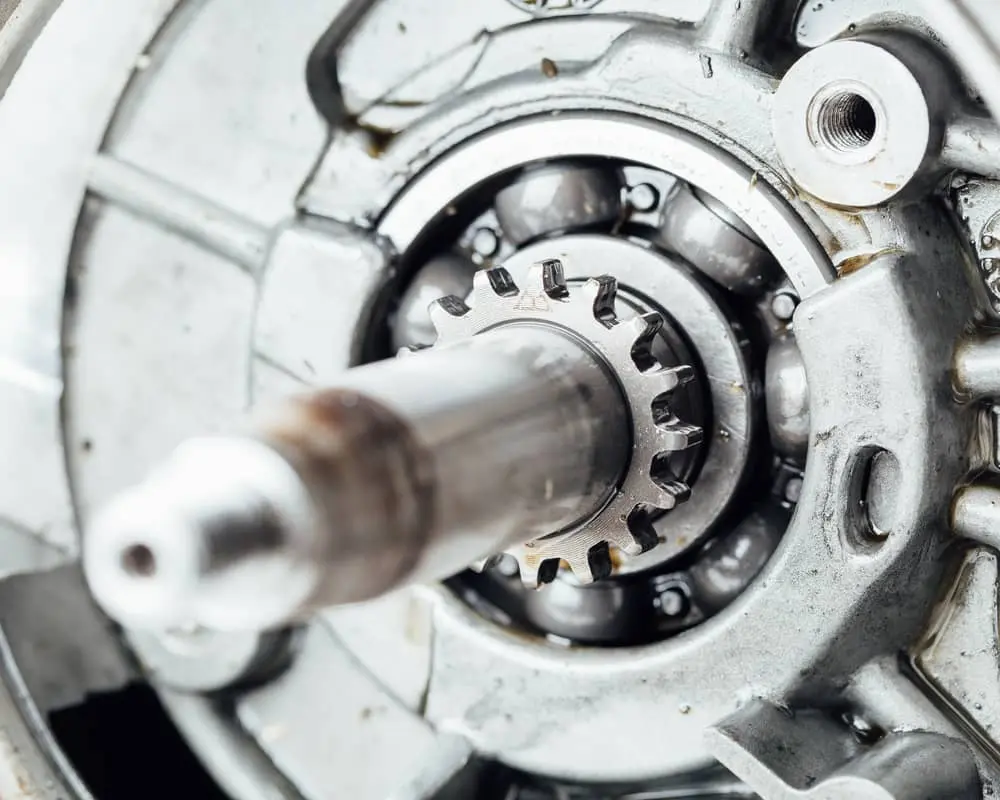
What Are The Symptoms of a Bad Shaft Bearing?
Bearing failure is a serious issue because spinning components in a machine can come grinding to a halt, leading to significant damage. Fortunately, several common symptoms allow the detection of a bearing failure before it is too late.
What are the symptoms of a bad shaft bearing? The first sign of bearing failure is excessive vibration. Following this, the bearing will heat up past acceptable levels and produce excessive noises, either high-pitched or grinding.
What are the Causes of Bad Shaft Bearing?
Metallurgical/Manufacturing Process Flaws
Occasionally, there are flaws in the metal or manufacturing process that can cause shafts to fail prematurely.
When a pump shaft breaks, the natural reaction is to blame the manufacturer. But in reality, shaft breakage is more often a direct result of the pump’s operating conditions. Only a tiny percentage of shaft failures are due to manufacturing flaws.
Vibration
Vibration is commonly caused by cavitation, critical speed, passing vane frequency, and operating outside the pump’s best efficiency point. Pump bearings begin to wear, allowing the shaft to move laterally, causing it to flex and eventually fail. The vibration harmonics also put extra stress on the pump shaft.
Imbalance
Imbalance creates problems while the pump runs, though the shaft will measure straight if stopped. It’s a vibration source that reduces the machine’s life, bearing, and mechanical seal.
Impeller imbalance is caused by the following:
- New, never-balanced impeller
- Trimmed and not balanced impeller
- Foreign objects stuck in vanes
- Vanes bent or out of a plane
- Balance holes plugged
- Product build-up on the impeller
Misalignment
Poor installation, pipe strain, extreme belt tension, and sheave misalignment on direct-drive pumps all put undue stress on a pump’s bearings and shaft.
Note that in a misalignment scenario, the pump’s bearings are more likely to fail before the shaft does. Nonetheless, we’ve included it here because misalignment creates bending moments for the shaft, weakening it over time.
Fluid Properties
When a pump is selected to move lower-viscosity fluids but subjected to higher-viscosity fluids, the likelihood of shaft breakage is higher. Be mindful of fluids that experience changes in viscosity due to temperature or being at rest. Fluids/slurries that dewater as they sit, such as paper stock, can also be problematic.
Hydraulic Shock
Hydraulic forces can cause serious damage. For example, a massive shock wave results when a check valve slams shut, interrupting fluid flow. This shock wave reverses flow and travels back downstream. When the shock wave collides with a pump, the shaft can bend or break instantly or over time, assuming the shock is strong enough.
Reverse Flow
What happens when reverse flow causes a pump’s impeller and shaft to turn backward, and the pump suddenly kicks on? You have a stressed or broken shaft. This scenario occurs when check valves upstream are partially or completely plugged or are not functioning properly.
What Are the Symptoms of a Bad Shaft Bearing?
There are five main bearing failure symptoms:
- Temperature: During operation, the bearing’s temperature rises above acceptable levels.
- Vibration: Excessive vibration occurs during operation.
- Lubrication: There is an improper bearing lubrication, meaning there needs to be more lubrication, too much lubrication, or the wrong lubrication has been used.
- Contamination: The lubricant has become contaminated with foreign particles or substances.
- Noise: There is excessive noise during operation, typically a high-pitched squealing or grinding sound.
Temperature
Bearings heat up during operation. An acceptable bearing temperature for many bearings is 82 ยฐC (180 ยฐF) or lower (please look at the bearing manual for product-specific temperature ratings). Because a bearing reduces frictional forces between rotating machine parts, a failing or failed bearing leads to more friction and higher operating temperatures. Therefore, regular temperature testing using temperature sensors, such as an infrared temperature sensor, is necessary. If an abnormally high temperature is detected, it is a sign to replace the bearing before it fails.
Vibration
Several reasons can cause excessive vibration from a failed bearing. For example, abrasion can damage the raceway, causing the rolling elements to bounce around. Slight differences between individual rolling elements caused by machining errors during bearing manufacturing can also lead to vibration. Various tools and methods are designed to test bearing vibration. If you notice abnormal vibration that has increased over time, it is typically a good indicator that the bearing should be replaced.
Lubrication
The most common reason for bearing failure is due to lack of lubrication. Bearings require precise lubrication to operate correctly. The bearing can fail from the following:
- Not enough lubrication can increase friction, leading to excessive wear and heat.
- Too much lubrication can increase pressure, leading to a seal failure, lubrication leak, and excessive heat generation.
- The wrong lubricant type can increase friction, leading to excessive wear and heat.
- Contaminated lubricant can increase friction, leading to excessive wear and heat.
Always check the bearing’s manufacturer’s instructions before conducting any lubrication-related maintenance.
Contamination
Bearing contamination can occur in several ways. One of the most common ways is during relubrication maintenance. Poor seals can allow foreign contaminants to mix with the lubricant. Also, high-pressure washing of a bearing can emulsify the lubricant. Ultimately, contaminants lead to abrasion, greatly reducing the bearing’s lifetime. If any contaminants are seen while inspecting the bearing, it should be replaced.
Noise
Failing bearings can make unusual noises, such as high-pitched squealing or grinding noises. The best method for using noise to indicate bearing failure is subjective. Pay attention to the noises of a properly functioning bearing to know when something sounds wrong.
Mounting and Installation of Bearings
It is vital in the mounting and installation process to pay close attention to the following:
- Use of proper tools and induction heaters/ovens. Use a sleeve to affect the entire inner ring face of the ring that is being pressed fit.
- Verify the shaft and housing tolerances. If the fit is too tight, too much preload is created. If the fit is too loose, too little resulting preload may allow the shaft to creep or rotate in the bearing. Check for proper roundness, diameters, and chamfer radius.
- Avoid misalignment or shaft deflection. This is especially critical in mounting bearings with separable components, like cylindrical roller bearings, where optimal life and successful load bearing are diminished or established at installation.
- Be conscious of radial internal clearance. It is critical to maintain the proper RIC established in the original design. The standard scale for ascending clearance is C2, C0, C3, C4, and C5. The right clearance for the application is crucial in that it allows for the challenges of:
- Lubrication. A right film of lubricant must be established between the rolling elements. Lessening internal clearance and impeding lubricant flow can cause premature failure.
- Shaft fit. A reduction in the radial internal clearance is inevitable when the bearing is press fit.
- Heat. In normal bearing operation, heat creates a thermal expansion of the inner and outer rings. This can reduce the internal clearance, reducing the optimal bearing life.
Operational Stress and Bearing Selection
Finding a bearing improperly designed into an application is generally the exception. However, factors within the larger application might change.
If loads become too high, early fatigue and overloading may follow. If they’re too low, skidding and improper loading of the rolling elements occur. In each situation, early failure will follow. Similar problems arise with improper internal clearance.
The initial sign of these issues will be unusual noises and increased temperatures.
Increased temperature. Bearing temperature often rises with start-up and stabilizes at a temperature a bit lower than at start-up (typically 10 to 40 degrees C higher than room temperature). The desired bearing temperature is below 100 degrees C.
Noises. Abnormal bearing sounds typically indicate certain problems in the bearing application. While this is a subjective test, it’s helpful to know that a howl or screech sound generally indicates too large a poor lubrication or internal clearance on a cylindrical roller bearing; on the other hand, a crunching felt when the shaft is rotated by hand often indicates raceways contamination.
Operational stresses in the applications can also affect bearing life. It is vital to isolate vibrations in associated equipment, as they can lead to uneven running and unusual noises.